Panthera Dental’s CAD/CAM Sub Implant is adaptable to specific bone morphology thanks to 3D imaging and printing technologies.
Marc Desjardins discusses a new implant that is adaptable to specific bone morphology
Since the arrival of conventional screw implants, subperiosteal implants have been relegated to the status of antiques! Frankly, their success rate, both surgically and prosthetically, was absolutely not comparable to the screw implants of today.
In previous years, the clinician had to be satisfied with prefabricated parts that often did not match the patient’s bone morphology. No auxiliary part was available for making the prosthetic part, no impression transfers, no abutments or implant replicas. The shape of these implants — often blade-shaped or with abutments that were too thin or too long — made it very difficult to achieve an accurate master model. Too often breakage occurred during the mold release. The fabrication of the prosthesis was also problematic.
Today different treatment plans can be considered in a situation where the patient’s mandible has a severely vertically atrophied posterior alveolar bone. Some treatment plans are indicated by the type of implant and the patient’s bone morphology. Others are adequate but are sensitive to the technique of the surgeon and require two surgeries. Only one meets all the criteria necessary for a predictable success — the CAD/CAM Sub Implant™ developed by Panthera Dental.
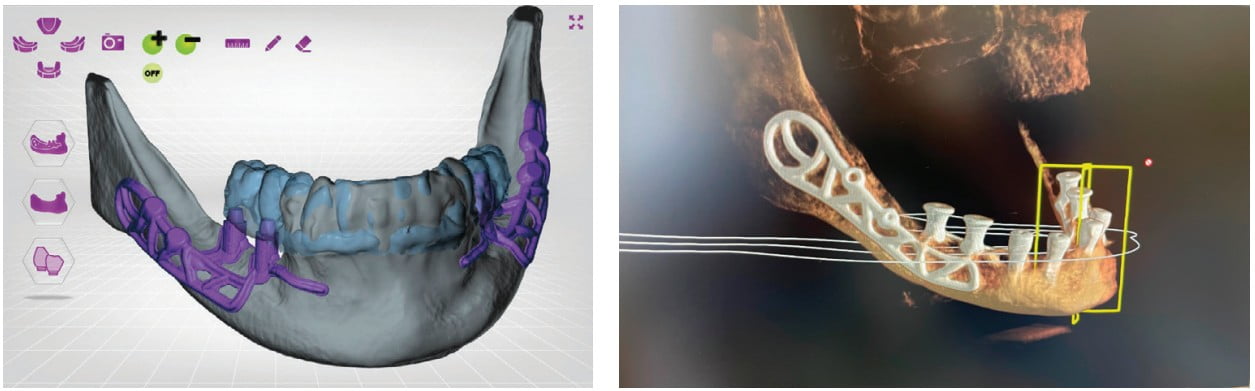
Using proven 3D imaging and printing technologies, the CAD/CAM Sub Implant from Panthera adapts perfectly to the specific bone morphology of each patient and can be placed in a single surgical phase. The abutments are always parallel to each other and offer a wide range of prosthetic components. Impression copings are available for open- or closed-impression trays. Of course, replicas complete the system. The conception of the prosthesis in the laboratory is therefore carried out in a completely conventional manner, ensuring absolute confidence in the final result.
This unique system is designed and manufactured from the CBCT scan of the patient and based on the optimal prosthetic treatment plan decided before the design of the implant. Once Panthera Dental receives it, the design is done in Panthera’s proprietary software and then manufactured in Grade 23 6AL 4V ELI titanium and sandblasted to optimize osseointegration. This process eliminates inaccuracies because no impressions of the bone can be as precise. As a result, the procedure is done quickly and requires only one surgery.
Several solutions are available to the dental technician depending on the patient’s particular situation — fixed, cemented, or completely removable prosthesis. In some cases, structures can even be manufactured and delivered simultaneously, reducing the waiting time and the number of appointments.
The Panthera CAD/CAM Sub Implant is the modern alternative solution for patients with lack of bone in the posterior area without sacrificing their healthy anterior teeth and their quality of life. In addition, the production of the prosthesis is part of a normal, conventional process that becomes a key element in the confidence of the dentist and patient.
This information was provided by Panthera Dental.
Panthera Dental helped to provide face shields to hospitals and non-profit organizations in Canada during the COVID-19 crisis. Read about this humanitarian project here: https://implantpracticeus.com/industry-news/250000-face-shields-delivered-mission-accomplished-for-panthera-dental/
Stay Relevant With Implant Practice US
Join our email list for CE courses and webinars, articles and mores